“Color coding”
is used in electronics to identify between different components. In the
case of resistors, color coding is used to identify a specific
resistance value, for example a 100 ohms resistor or a 1 kilo ohms
resistor with 5% tolerance. Electronic components like resistors are
very small in size and its difficult to print its value directly on to
the component surface. Hence a standard was formed in 1920 by then Radio
Manufacturers Association (now part of EIA – Electronic Industries
Alliance) to identify values and ratings of electronic components by
printing color codes on them. Color coding technique makes it easy to
print values (based on color codes) on small components, such as
resistors and facilitates cost effective manufacturing.
This technique of
“color coding” has 2
disadvantages. The first one appeals to general users where it becomes
difficult to distinguish between colors (for example “Red” and “Brown” )
when the component is over heated. But this is not a major concern as
the exact value can be easily identified using a multimeter (in case of
confusion). The next drawback is for a specific group of people – color
blind people can not identify the device using color codes. However they
too can depend on multimeter to identify resistance values.
How to Identify Resistor Color Code
The figure below shows the layout of the bands, the multiplier and
the tolerance value of a resistor. For a 6-band resistor, an additional
temperature coefficient band is provided.
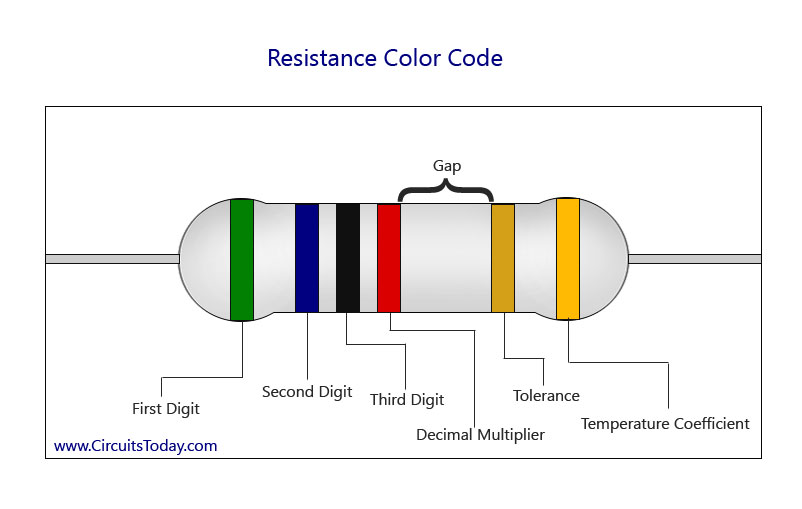
The gap between the multiplier and the tolerance specifies the left and right side of the resistor. So here are the key points;
4 band resistor – has 3 color bands on left side and
one color band on right side. First two bands represent significant
digits, the 3rd band represents multiplier and the fourth band on right
side represents tolerance.