When a sample of crystalline silicon is
covered with silicon dioxide, the oxide-layer acts as a barrier to the
diffusion of impurities, so that impurities separated from the surface
of the silicon by a layer of oxide do not diffuse into the silicon
during high-temperature processing. A p-n junction can thus be formed in
a selected location on the sample by first covering the sample with a
layer of oxide [oxidation step] removing the oxide in the selected
region, and then performing a predeposition and diffusion step. The
selective removal of the oxide in the desired area is performed with
photolithography. Thus, the areas over which diffusions are effective
are defined by the oxide layer with windows cut in it, through which
diffusion can take place. The windows are produced by the
photolithographic process. This process is the means by which
microscopically small electronic circuits and devices can be produced on
silicon wafers resulting in as many as 10000 transistors on a 1 cm x 1
cm chip.
In fact photolithography or optical
lithography is a kind of lithography. The lithography technique was
first used in the late 18th century by people interested in
art. A lithograph is a less expensive picture made from a flat,
specially prepared stone or metal plate and the lithography is art of
making lithographs. Therefore, lithography for IC manufacturing is
analogous to the lithography of the art world. In this process the
exposing radiation, such as ultraviolet (UV) light in case of
photolithography, is transmitted through the clear parts of the mask.
The circuit pattern of opaque chromium blocks some of die radiation.
This type of chromium/glass mask is used with UV light. Other types of
exposing radiations are electrons, X-rays, or ions. Thus for IC
manufacturing we have following types of lithography. Photolithography
has been explained in this post. To know about the other types of
lithographic process, click on the link below.
- Photolithography
- Electron-beam Lithography
- X-ray lithography
- Ion-beam lithography
In IC fabrication a number of masks are
employed. Except for the first mask, every mask must be aligned to the
pattern produced by the previous mask. This is done using mask aligner.
The mask aligner may be contact type or proximity type or projection
type. Accordingly we have three types of printing. They are
- Contact printing
- Proximity printing
- Projection printing
Photolithographic Process Steps
1. Photoresist Application (Spinning)
A drop of light-sensitive liquid called
photoresist is applied to the centre of the oxidized silicon wafer that
is held down by a vacuum chuck. The wafer is then accelerated rapidly to
a rotational velocity in the range 3000 to 7000 RPM for some 30 to 60
seconds. This action spreads the solution in a thin, nearly uniform coat
and spins off the excess liquid. The thickness of the coat so obtained
is in the range 5000 to 10000 A, as shown in the figure below. The
thickness of the photoresist layer will be approximately inversely
proportional to the square root of the rotational velocity.
Sometimes prior to the application of
the photoresist the silicon wafers are given a “bake-out” at a
temperature Of at least 100°C to drive off moisture from the wafer
surfaces so as to obtain better adhesion of the photoresist. Typical
photoresist used is Kodak Thin Film Resist (KTFR).
2. Prebake
The silicon wafers coated with
photoresist are now put into an oven at about 80°C for about 30 to 60
minutes to drive off solvents in the photoresist and to harden it into a
semisolid film.
3. Alignment and Exposure
The coated wafer, as above, is now
placed in an apparatus called a mask aligner in very close proximity
(about 25 to 125 micro meters) to a photomask. The relative positions of
the wafer and the photomasks are adjusted such that the photomask is
correctly lined up with reference marks or a pre-existing pattern on the
wafer.
The photomask is a glass plate,
typically about 125 mm square and about 2 mm thick. The photomask has a
photographic emulsion or thin film metal (generally chromium) pattern on
one side. The pattern has clear and opaque areas. The alignment of the
photomask to the wafer is often required to be accurate to within less
than 1 micro meter, and in some cases to within 0.5 micro meters. After
proper alignment has been achieved, the wafer is brought into direct
contact with the photomask. Photomask making will be described
separately.
A highly collimated ultraviolet (UV)
light is then turned on and the areas of the silicon wafer that are not
covered by the opaque areas of the photomask are exposed to ultraviolet
radiation, as shown in the figure. The exposure time is generally in the
range 3 to 10 seconds and is carefully controlled such that the total
UV radiation dosage in watt-seconds or joules is of the required amount.
4. Development
Two types of photoresist exist- negative
photoresist and positive photoresist. In the present description
negative photoresist is used in which the areas of the photoresist that
are exposed the ultraviolet radiation become polymerized. The
polymerization process increases the length of the organic chain
molecules that make up the photoresist. This makes the resist tougher
and makes it essentially insoluble in the developer solution. The
resisting photoresist pattern after the development process will
therefore be a replication of the photomask pattern, with the clear
areas on the photomask corresponding to the areas where the photoresist
remains on the wafers, as shown in the figure below.
An opposite type of process occurs with
positive photoresist. Exposure to UV radiation results in
depolymerization of the photoresist. This makes these exposed areas of
the photoresist readily soluble in the developer solution, whereas the
unexposed areas are essentially insoluble. The developer solution will
thus remove the exposed or depolymerized regions of the photoresist,
whereas the unexposed areas will remain on the wafer. Thus again there
is a replication of the photomask pattern, but this time the clear areas
of the photomask produce the areas on the wafer from which the
photoresist has been removed.
5. Postbake
After development and rinsing the wafers
are usually given a postbake in an oven at a temperature of about 150°C
for about 30 to 60 minutes to toughen further the remaining resist on
the wafer. This is to make it adhere better to the wafer and to make it
more resistant to the hydrofluoric acid [HF] solution used for etching
of the silicon dioxide.
6. Oxide Etching
The remaining resist is hardened and
acts as a convenient mask through which the oxide layer can be etched
away to expose areas of semiconductor underneath. These exposed areas
are ready for impurity diffusion.
For etching of oxide, the wafers are
immersed in or sprayed with a hydrofluoric [HF] acid solution. This
solution is usually a diluted solution of typically 10: 1, H2O : HF, or more often a 10 : 1 NH4F [ammonium fluoride]: HF solution. The HF solutions will etch the SiO2
but will not attack the underlying silicon, nor will it attack the
photoresist layer to any appreciable extent. The wafers are exposed to
the etching solution ion enough to remove the SiO2 completely in the areas of the wafer that are not covered by the photoresist as shown in the figure.
The duration of oxide etching should be
carefully controlled so that all of the oxide present only in the
photoresist window is removed. If etching time is excessively prolonged,
it will result in more undercutting underneath the photoresist and
widening of the oxide opening beyond what is desired.
The above oxide etching process is termed wet etching process since the chemical reagents used are in liquid form. A newer process for oxide etching is a dry etching process called plasma etching. Another dry etching process is ion milling.
7. Photoresist Stripping
Following oxide etching, the remaining
resist is finally removed or stripped off with a mixture of sulphuric
acid and hydrogen peroxide and with the help of abrasion process.
Finally a step of washing and drying completes the required window in
the oxide layer. The figure below shows the silicon wafer ready for next
diffusion.
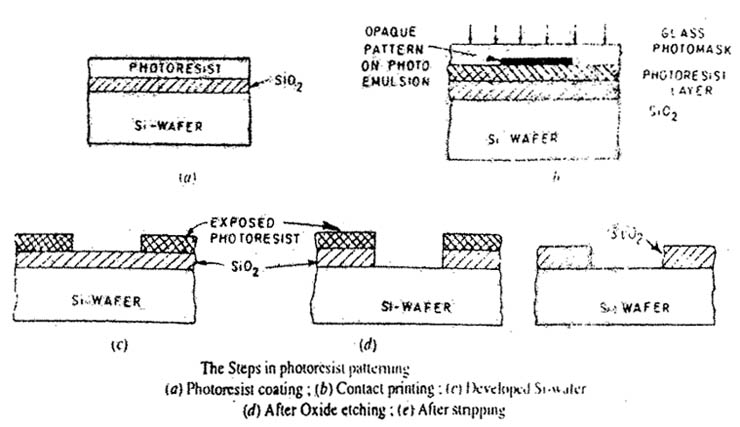
Photolithographic Process Steps
The photolithography may employ contact,
proximity, or projection printing. For IC production the line width
limit of photolithography lies near 0.4 micro meters, although 0.2 micro
meters features may be printed under carefully controlled conditions.
At present, the photolithography occupies the primary position among
various lithographic techniques.
Photoresists
One of the major factors in providing
increasingly complex devices has been improvement in photolithographic
art. A large part of this improvement has been due to high quality
photoresist, materials as improved techniques of coating, baking,
exposing and developing photoresists.
The principal constituents of a
photoresist solution are a polymer, a sensitizer and a suitable solvent
system Polymers have properties of excellent film forming and coating.
Polymers generally used are polyvinyl cinnamate, partially cyclized
isoprene family and other types are phenol formaldehyde.
When photoresist is exposed to light,
sensitizer absorbs energy and initiates chemical changes in the resist.
The sensitizers are chromophoric organic molecules. They greatly enhance
cross linking of the photoresist. Cross linking of polymer or long
chain formation of considerable number of monomers makes high molecular
weight molecules on exposure to light radiation, termed as
photo-polymerization. Typical sensitizers are carbonyl compounds,
Benzoin, Benzoyl peroxide, Benzoyl disulphide, nitrogen compounds and
halogen compounds.
The solvents used to keep the polymers
in solution are mixture of organic liquids. They include aliphetic
esters such as butyl acetate and cellosolve acetate, aromatic
hydrocarbons like xylene and Ethylbenzene, chlorinated hydrocarbons like
chlorobenzene and methylene chloride and ketones such as cyclohexanone.
The same solvents are used as thinners and developers.
Characteristics of Good Photoresist
To achieve faithful registration of the
mask geometry over the substrate surface, the resist should satisfy
following conditions.
- Uniform film formation
- Good adhesion to the substrate
- Resolution
- Resistance to wet and dry etch processes
Types of Photoresist
Polymers film is either photosensitive
or capable or reacting with the pholysis product of additional compound
so that the solubility increases or decreases greatly by exposure to UV
(ultra-violet) radiation. According to the changes that take place,
photoresists are termed negative or positive. Materials which are
rendered less soluble in a developer solution by illumination^ yield a
negative pattern of the mask and are called negative photoresists.
Conversely, positive photoresists become more soluble when subjected to
light and therefore yield a positive image of the mask.
Negative Photoresist
Kodak negative photoresist contain
polyvinyl cinnametes. KPR is being used in printing circuit boards. KTFR
is widely used in fabrication of ICs. It provides good adhesion to
silicon dioxide and metal surfaces. It gives well etch results to
different etchant solutions. For finer resolution, thinner coating of
KTFR is used. To achieve controlled and uniform thickness, the viscosity
of resist is suitably lowered using thinners.
Another negative photoresist is Kodak
Microneg 747 which provides high scan speeds at high aperature giving
high throughput and resolution.
Positive Photoresist
Positive Photoresists have solved the
problem of resolution and substrate protection. Photo resists can be
used at a coating thickness of 1 micro meter that eliminates holes and
minimises defects from dust.
Positive photoresist is inherently of
low solubility (polymerized) material. The base polymer is active by
itself. A sensitizer, when absorbs light, makes the base resist soluble
in an alkali developer. Positive photoresists are Novolac resins.
Typical solvents are cellosolve acetate, butyl acetate, xylene and
toluene.
Resist requirements for VLSI
For fine line geometries in VLSI
circuits, the resist requirements become more stringent. The resist
properties should meet the required demand of high resolution. Here the
resist should exhibit
- High sensitivity for partial exposure tool chosen
- Dry developing, dry compatibility
- Vertical profile control
Photomask Fabrication
Photolithography is used to produce
windows in the oxide layer of the silicon wafer, through which diffusion
can take place. For this purpose photomask is required. In this section
we shall discuss various techniques of mask fabrication. The pattern
appearing on the mask is required to be transferred to the wafer. For
this purpose various exposure techniques are employed. We will also
discuss these techniques.
Mask Making
IC fabrication is done by the batch
processing, where many copies of the same circuit are fabricated on a
single wafer and many wafers are fabricated at the same time. The number
of wafers processed at one time is called the lot size and many vary
between 20 to 200 wafers. Since each IC chip is square and the wafer is
circular, the number of chips per wafer is the number of complete
squares of a given size that can fit inside a circle.
The pattern for the mask is designed
from the circuit layout. Many years ago, bread boarding of the circuit
was typical. In this, the circuit was actually built and tested with
discrete components before its integration. At present, however, when
LSI and VLSI circuits contain from a thousand to several hundred
thousand components, and switching speeds are of such high order where
propagation delay time between devices is significant, bread boarding is
obviously not practical. Present-day mask layout is done with the help
of computer.
The photographic mask determines the
location of all windows in the oxide layer, and hence areas over which a
particular diffusion step is effective. Each complete mask consists of a
photographic plate on which each window is represented by an opaque
are, the remainder being transparent. Each complete mask will not only
include all the windows for the production of one stage of a particular
IC, but in addition, all similar areas for all such circuits on the
entire silicon as shown in the figure below.
It will be obvious that a different mask
is required for each stage in the production of an array of IC’s on a
wafer. There is also a vital requirement for precise registration
between one mask and the other in series, to ensure that there is no
overlap between components, and that each section of a particular
transistor is formed in precisely the correct location.
To make a mask for one of the production
stages, a master is first prepared which is an exact replica of that
portion of the final mask associated with one individual integrated
circuit, but which is 250x [say] enlargement of the final size of IC.
The figure below shows a possible master for the production of a mask to
define a particular layer of diffusion for a hypothetical circuit. Art
work at enlarge size avoids large tolerance errors. Large size also
permits the art work to be dealt easily by human operator. In the design
of the art work, the locations of all components that is, resistor,
capacitor, diode, transistor and so on, are determined on the surface of
the chip. Therefore, six or more layout drawings are required. Each
drawing shows the position of Windows that are required for a particular
step of the fabrication. For complex circuit the layout is generated by
the use of computer-aided graphics.
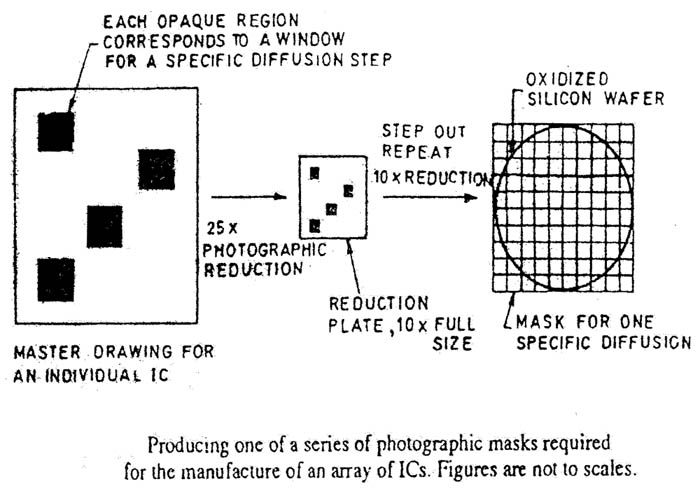
Photomask Fabrication
The next step is to photograph the
master using back illumination, to produce a 25 x reduced sub-master
plate. This plate is used in a step and repeat camera which serves the
dual purpose of reducing the pattern by a further 10 x to finished size
and is also capable of being stepped mechanically to produce an array of
identical patterns on the final master mask, each member of the many
corresponding to one complete IC. Instead of the photographic plate
being transported mechanically in discrete steps, better accuracy may be
achieved by using continuous plate movement; discrete exposures then
being made by an electronically synchronized flash lamp which
effectively freezes the motion.
The entire sequence just described can
be done with plates containing a photosensitive emulsion; typically the
emulsion is considered too vulnerable to abrasion and tears. For this
reason, masks are often made of harder materials such as chrome or iron
oxide.
For very complex circuits automated mask
generation equipment is used. In this, a computer controlled light
flashes to build up the pattern on a photographic film by a series of
line or block exposures, the resulting film is then reduced and handled
in a step and repeat system to create the production mask.
Alternatively, the master mask can be generated by an electron beam
exposure system, again controlled by computer.
Various Printing Techniques
Photolithography comprises the formation
of images with visible or U V radiation in a photoresist using contact
proximity, or projection printing. Here we will discuss about these
printing techniques.
1. Contact Printing
In this printing technique, the
photomask is pressed against the resist coated wafer with a pressure
typically in the range of 0.05 atm to 0.3 atm and exposure by light of
wavelength near 400 micro meters. A resolution of less than 1 micro
meter linewidth is possible, but it may vary across the wafer because of
spatial non-uniformity of the contact. To provide better contact over
the whole wafer, a thin (0.2 mm) flexible mask has been used.
2. Proximity Printing
In proximity or shadow
printing, there exists a gap between mask and wafer in the range of 20
to 50 micro meters. This has the advantage of longer mask life because
there is no contact between the mask and the wafer. In the proximity
printing, the mask and wafer are both placed in an equipment called a
projection aligner. Looking through a microscope, an operator brings the
mask into close proximity [say 10 to 20 micro meters] to the wafer and
properly aligns the wafer and mask using alignment mark on the mask and
the wafer. UV light is then projected through the mask on to the entire
resist coated wafer at one time. This mask that is used is a full wafer x
1 mask. The resolution of this process is a function of the wavelength
of the light source and the distance between the mask and the wafer.
Typically, the resolution of proximity printing is 2 to 4 micro meter
and is therefore not suitable for a process requiring less than a 2 um
minimum line width.
3. Projection Printing
In this case the image is actually
projected with the help of a system of lenses, onto the wafer. The mask
can be used a large number of times, substantially reducing the mask
cost per wafer. Theoretically a mask can be used an unlimited-number of
times, but actual usage is limited to about 100,000 times because the
mask must be cleaned due to dust accumulation, and it is scratched at
each cleaning. This is costliest of the conventional systems, however
mask life is good, and resolution obtained is higher than proximity
printing together with large separation between mask and wafer.
Automated Mask Generation
As discussed above, layouts of
electronic circuit are drawn on large mylar sheets. They can also be
drawn on a CRT screen by which layouts are stored digitally in a
magnetic tape (or disk). In this case we need to prepare many layouts
since each layout represents a pattern on each mask to be used during
fabrication. Since the layouts are to be stored digitally, it is
required to convert the layouts drawn on mylar sheets into digital data.
This is performed by a digitizer with the aid of a computer. Then
different portions of each layout are displayed on a CRT one by one and
inspected for further mistakes. After all the corrections have been
made, a reticle, which is a small photographic plate of the layout
image, is prepared from each layout stored on the magnetic tape.
Depending upon the type of equipment
used, the mask to be fabricated contains one IC chip pattern which is
repeated as many times as there are on the wafer. Alternatively, the
mask consists of only magnified chip pattern as shown in the figure
below.
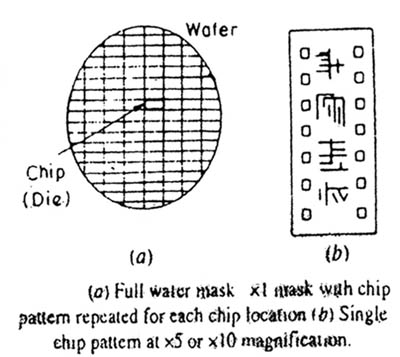
Automated Mask generation
- Using optical projection and
- Using electron beam
A pattern generator (PG) tape is used as
the Input to both approaches. The PG tape, contains the digitized data
necessary to control the light source or electron beam that is used to
write a pattern on a photosensitive glass plate. An Ax10 pattern for a
single chip (called a x10 reticle) is first produced. This reticle is
then photo enlarged by a factor of 15, yielding x 150 blowback, which is
used for visual checking. A x 1 mask of the type shown in the figure
is then produced from the x 10 reticle by optical reduction and
projection onto a second photosensitive plate. The same pattern is
stepped and repeated on this plate as many as there are chips on the
wafer. This step and repat operation is performed by photo repeater. The
glass plate is then developed yielding a x 1 mask which is called a
master mask and looks like a tile floor where each rectangular tile has
the same layout image of the chp. During the step and repeat process the
position and angle of the reticle are precisely aligned with the help
of two fiducial marks incorporated in the PG files of all layouts in the
same relative position with respect to the entire chip. The master mask
plate is then placed in close proximity to the wafer and optically
projected on to a resist-coated wafer during the lithographic process.
The figure below shows the second
approach. This employs electron-beam mask generation equipment winch
generates the mask plate in one step. The layout data are converted into
a hit map of 1’s and 0’s on a raster image. The electron beam sweeps
the row in a repeating S pattern, blanking or unblanking the beam
according to the input bit value, 0 or 1. In the figure, the x10 reticle
is optically reduced and stepped directly onto the wafer. This is
referred to as direct-step on wafer (DSW) lithography.
Automated Mask Generation Process
No comments:
Post a Comment